Metal Injection Molding(MIM)
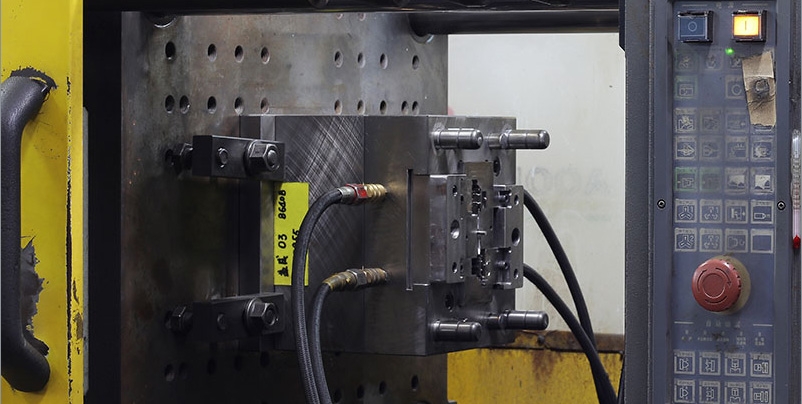
Introduction to MIM Machining
What is MIM Machining?
Metal Injection Molding (MIM) is an innovative manufacturing process that combines the versatility of plastic injection molding with the strength and durability of metal. This technique allows for the production of complex, high-precision metal parts by mixing fine metal powders with a binding agent to create a feedstock. The mixture is then injected into molds, where it undergoes a series of processes to form solid metal components. MIM is particularly advantageous for producing small, intricate parts that require high dimensional accuracy.
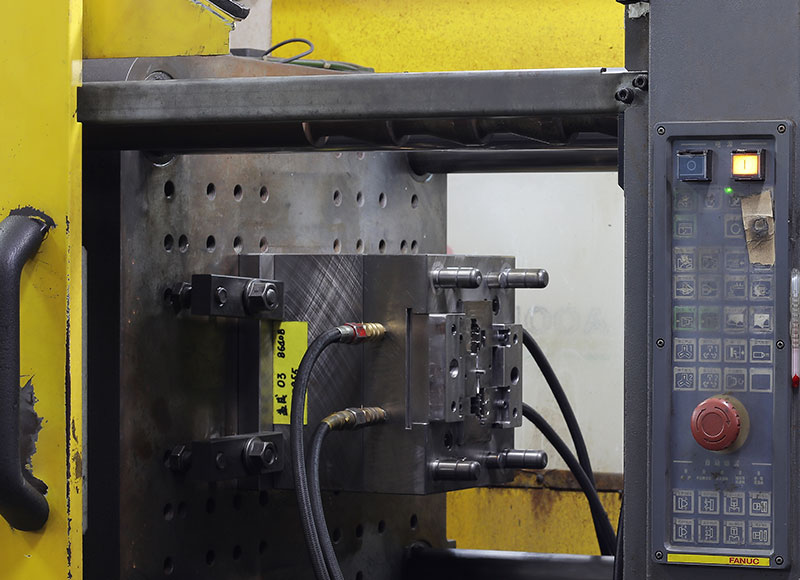
Comparison: MIM Machining vs Traditional Machining
When comparing MIM machining to traditional machining methods, several key differences emerge:
- Complexity: MIM excels in producing complex geometries that are often challenging or impossible to achieve with traditional machining techniques.
- Cost Efficiency: For medium to high production volumes, MIM is generally more cost-effective than CNC machining, which can be expensive for intricate designs due to higher labor and material waste.
- Material Utilization: MIM minimizes waste by using near-net-shape processing, whereas traditional machining often results in significant material loss as it involves cutting away material from larger blocks.
MIM Machining Process and Benefits
MIM Machining Process: Step-by-Step
- Powder Preparation: Fine metal powders are mixed with a binding agent to create a feedstock.
- Injection Molding: The feedstock is injected into molds under high pressure to form the desired shape.
- Debinding: The binding agent is removed through thermal or solvent processes.
- Sintering: The molded parts are heated in a furnace, causing the metal particles to fuse together, resulting in a solid component.
Materials Used in MIM Machining
MIM can utilize a wide range of materials, including:
- Stainless Steel (e.g., 316L)
- Tool Steel
- Chromium Molybdenum Steel
- Iron-Nickel Alloy
Benefits of MIM Machining
- Design Flexibility: MIM allows for intricate designs and features like threads and cavities that are difficult to achieve with traditional methods.
- High Density and Strength: Sintered parts typically reach over 95% of the density of wrought metals, resulting in excellent mechanical properties.
- Cost Reduction: The ability to produce complex shapes in one step reduces the need for secondary operations, lowering overall production costs.
- Sustainability: Minimal material waste and lower energy consumption make MIM an environmentally friendly option compared to traditional machining.
Applications of MIM Machining in Various Industries
MIM technology has found applications across several industries due to its efficiency and versatility:
- Medical Devices: Used for surgical instruments and implants requiring high precision.
- Aerospace: Produces components such as fuel system parts and engine components.
- Consumer Electronics: Ideal for small, complex parts found in various electronic devices.
- Automotive: Supplies high-strength components like gears and pulleys.
Gallery of JINHOLLY MIM Solutions
Why Choose Jinholly as a Reliable Partner?
Jinholly stands out as a trusted partner in the field of Custom Metal Injection Molding due to several strengths:
- Versatile Material Options: We work with various materials, including stainless steel and specialized alloys, ensuring we meet diverse client needs.
- Expertise in Complex Shapes: Our advanced mold design capabilities allow us to produce intricate 3D shapes efficiently.
- High Strength Products: Our manufacturing process ensures that products achieve high density and strength, making them suitable for demanding applications.
- Cost Efficiency: By minimizing CNC processing steps, we help reduce overall production costs while maintaining quality.
- Commitment to Collaboration: We are dedicated to working closely with clients on product development, ensuring fast and stable delivery of high-quality products.
If you’re looking for a reliable partner for your Metal Injection Molding needs, Jinholly is ready to assist you! Reach out today to discuss your project requirements and explore how we can help you achieve your manufacturing goals.
OEM / ODM Solution
Select appropriate processing methods for clients to help them reduce costs, achieve high efficiency, and high-quality service.